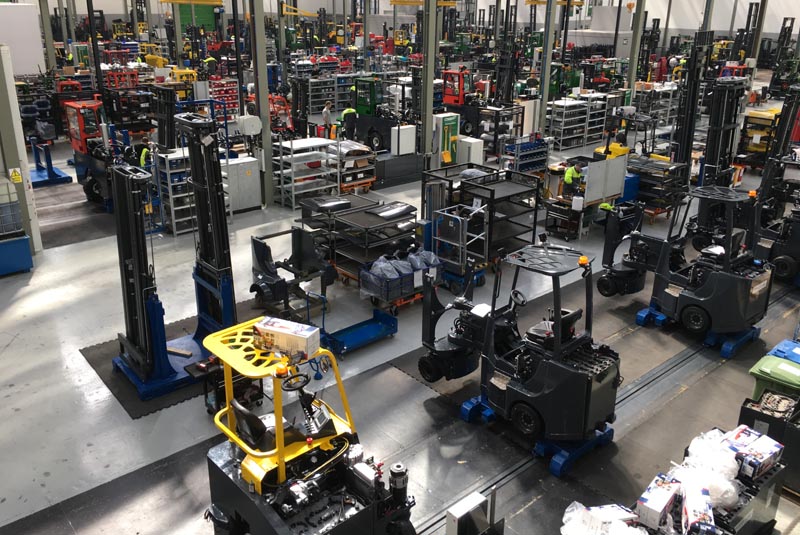
June 9th was National Forklift Safety Day in the UK and North America — an initiative to promote a safer working environment for all those who work with, on or near forklift trucks.
To mark the event and discuss the safety issues related to materials handling, Combilift hosted a Zoom conference with a number of media titles. Martin Mc Vicar, the firm’s co-founder and Managing Director, explained that since Combilift was established, a cornerstone of its design philosophy has been to supply innovative handling solutions that reduce risk and prevent accidents.
Indeed, Martin said that under this ethos of ‘safety through innovation’ and in addition to enabling space saving and productive handling of loads of various sizes and dimensions, more secure and safer handling is cited by many of the company’s customers as the reason why they opted for a Combilift product over other types of forklifts.
The company states that its commitment to safety has also been recognised by industry associations such as the Forklift Truck Association (FLTA) and British Industrial Truck Association (BITA), from whom it has received safety awards for its models or features that it has developed and incorporated into its products.
An overview of a number of these can be found on its website — whilst to mark the National Forklift Safety Day, it has been taking a closer look at some of its individual models throughout the week and explaining how the firm considers they contribute to enhanced safety procedures in the warehouse and other environments for loading and offloading materials.
Martin noted that from the outset, Combilift did not set out to make “regular forklifts” but instead has always concentrated on “developing products that solve particular logistical challenges”. Some 7% is annually invested into research and development, and many of the video features it is presenting show the perceived performance advantages of its own solutions against more traditional machines.
And whilst the company is perhaps best known for its multi-directional trucks and units specifically designed to handle long and awkward loads in restricted spaces, one of the products flagged in the video conference was the Combi-CS pedestrian truck.
The machine won the Industrial Vehicles Category of the BITA Design4Safety Awards for its “unique, patented multi-position tiller arm” — a feature common to all its pedestrian models.
It was designed to ensure maximum safety for the operator and other personnel who may be in the area where the trucks are operating, whilst enabling productive picking and placing of products in narrow aisles. The tiller arm can be turned to the left or right of the truck and enables push button rotation of the rear wheel parallel to the chassis and back again.
Accordingly, it allows the operator to remain in the safest possible position when working in narrow aisles — specifically, at the side of the truck rather than at the rear as is the case with other pedestrian trucks. This reduces the risk of the operator being crushed or trapped between the truck and the racking.
The video was filmed in a Homebase warehouse, however Martin specifically explained that such pedestrian forklifts could have a number of practical and safe uses within the builders’ merchant environment, and especially in areas shared by staff and customers.
Indeed, pedestrian trucks naturally operate at slower speeds compared to motorised ride-on forklifts, and operators have a heightened awareness of their immediate environment as well as good all-round visibility of the load and the forks.
However, high levels of performance remain essential and this is said to have underpinned the development of the Combi WR4 — described as the first purpose built 4-way pedestrian reach stacker which combines multi-directional travel with features such as a pantograph reach, side shift and tilting fork carriage for handling long loads and pallets.
It is said to be the only truck of its kind able to work in aisle-widths of 2.1m pallet to pallet and its excellent ergonomics, which enhance occupational health and safety for the operator, earned it an FLTA Award a few years ago.
Avoiding overloading
Overloaded vehicles can tip and fall, resulting not only in damage to vehicles and stock, but at worst can cause serious or fatal injuries to personnel. There are several factors that can influence a forklift truck to become overloaded and the load centre — the distance from the face of fork to the centre of gravity of the load — plays a crucial part.
Forklift operators who are insufficiently aware of their forklift’s load capacity and the risks that come with exceeding this not only compromise their own safety, but also place everyone working around them at serious risk. However, Combilift states that as “we cannot expect forklift operators to have to constantly do the maths, we need to make life easier — and safer — for them”.
The Combilift Safe-Lift is an anti-overload device which enables drivers to avoid the pitfalls of potential overloading. It incorporates a strain sensor on the mast and a lift cut-out valve positioned on the mast hydraulic lift hose. There is an audible alarm which warns the operator of an overload situation and an indicator unit is fitted to the dashboard in the cab.
The operator can instantly see from the green, amber and red ‘traffic light’ signalling when there is a risk of overloading or when the forks are not fully engaged for example and take appropriate action. Fitting this simple and cost effective system to counterbalance trucks, says Martin, is an effective way to cut risks for the operators and other personnel — and also to avoid product damage as well as costly repairs.