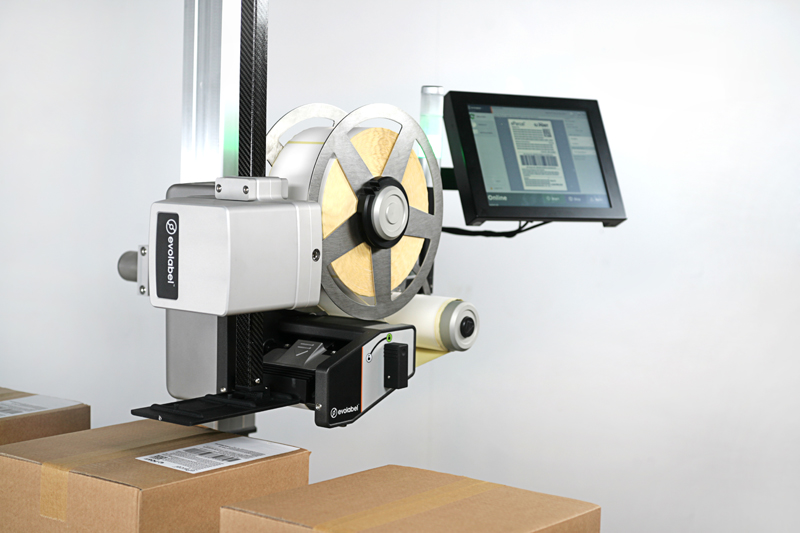
Denis Brett, Managing Director at Industrial Labelling Systems (ILS), explains how it is possible to tighten supply chains with durable, flexible and traceable labelling.
The construction industry is largely project-based with complex supply chains. It only takes one link to unravel for it to impact negatively on build schedules, cost forecasts and customer satisfaction.
There is a need for companies to pay attention to the finer aspects of their product supply chain — often starting with something as simple as accurate and reliable labelling of component parts and pallets. Having correctly labelled and traceable products is an intrinsic stage in managing the overall outcome of a build.
Construction can be a hostile environment for labels which means that they have to be robust enough to cope with challenging temperatures, rough handling and uneven stacking as well. Ensuring that product labelling is suited to the environment in which it is to be placed is crucial to the traceability of supplied materials.
Labelling that is designed to go on items such as pallets of bricks, paving stones, concrete and other aggregates must be puncture- and tear-resistant as well as giving a high level of conformity around irregular surfaces — i.e. do not wrinkle and distort product information.
Many builders’ merchants store aggregates and large products outside for lengthy periods. These materials not only need to have labels which can tolerate a wide range of weather conditions and handling by fork lift truck but also need to reliably provide key serial numbers, batch codes and barcodes that won’t fall off through wear and tear.
To achieve an uninterrupted supply chain and be confident of traceability, it is vital that producers choose a labelling system that is fully adapted to withstand harsh conditions and uses plastic coated (Polyethylene PE or Polypropylene PP) labels with strong adhesives guaranteed never to come off and to be fully readable for up to five years.
Advanced software features can also help with traceability as state-of-the-art print and apply labelling equipment is capable of generating and accurately positioning labels with a unique identity (a barcode for example). This enables products to comply with the GS1 SSCC barcodes regulation and ensures shipments, warehousing, and storage locations can be tracked and traced effectively.
Some labelling companies like Evolabel have engineered standard print and apply pallet labelling equipment to cope well in temperatures as low as -20°C without interruption to the production line and can be supplied with special covers for protection in dusty environments.
Correct pallet labelling can be achieved even when pallets are presented with non-uniform spacing or are unevenly stacked. A label applicator can be designed to swing in different directions — front, back and side as it detects the pallet moving past. It is possible for guiding brushes to be attached to ensure that the label is firmly secured and readable in its entirety — no matter how non-uniformly the product was originally presented on the conveyor.
Many labelling applicators include features offering label count and reconciliation of data that can usually be passed through third-party systems back to ERP software. Such systems dovetail into the print and apply labeller to enable smartphone apps to illustrate key performance indicators (KPIs) and dashboard data. The customer is also able to view the current status via web browsing.
To improve build effectiveness, companies have to improve predictability, optimise costs, mitigate risk and analyse data. Making strategic improvements at the very start of a project by choosing the most effective product labelling is sure to have a positive ‘ripple’ effect on final outcomes.
ILS is the exclusive UK distributor for Evolabel print and apply systems. For more information visit, www.ilsystems.co.uk.