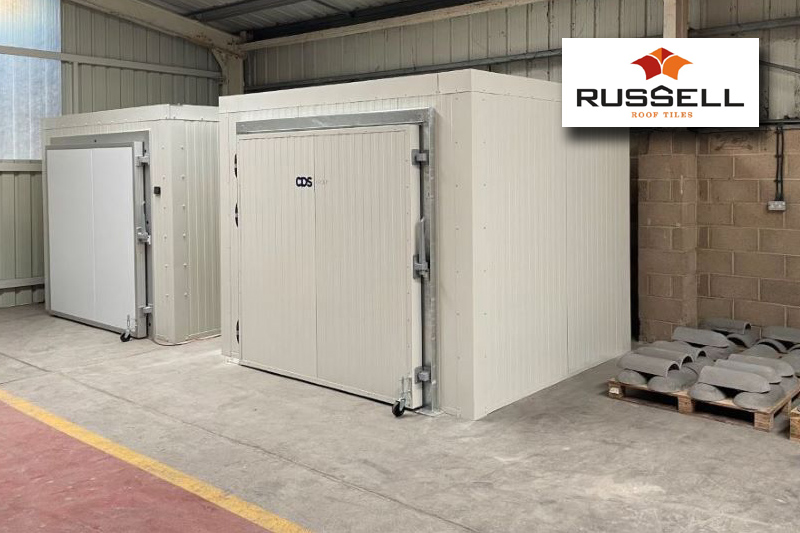
Due to the high demand for concrete roof tiles as the construction industry rises above pre-Covid levels, Russell Roof Tiles has seen a huge increase in the requirement for concrete hand-fittings and has taken steps to increase capacity.
The roof tile manufacturer has invested in two new curing chambers as part of a wider expansion programme, allowing it to increase capacity on certain key concrete hand fittings by 50%. With the key focus on Hip End and Block End Ridge concrete products, the investment will also allow the firm to produce more vent tiles and other handmade items.
The manufacturer worked closely with specialist curing contractors to design and build the two new chambers, which are now fully operational.
Dan Hancox, Business Support Manager at Russell Roof Tiles said: “Following our green agenda, the new curing chambers have been designed to be fully insulated and temperature-controlled units to ensure optimisation of energy consumption and reduce wasted heat. This means we can be more efficient with a lower carbon footprint.”
By investing in high tech temperature and humidity monitoring, Russell Roof Tiles says it is able to maintain the stability required to produce high quality products whilst adding additional volume to its existing product range and thereby supporting production facilities across all its sites – two in urton and Lochmaben, near Lockerbie in Scotland.
Dan explained: “The investment is to address the growing demand in the current climate and to provide greater flexibility in production. The main purpose of this project is to support Lockerbie to produce more fittings, but a large portion of these are sold in the Midlands – so we have moved some production to the local area to avoid extra transportation costs and save on the environment.”