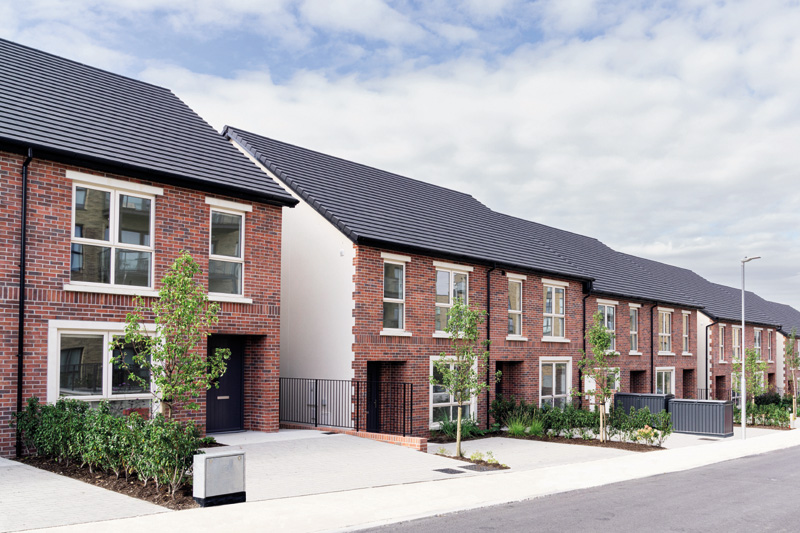
AG has announced an upgrading of its best-selling facing brick product, Woodward Brick.
The Woodward Fine Cast Facing Brick from AG has now been enhanced with Enduur 1, described as an advanced concrete technology that “delivers an impressive range of product enhancements from increased strength, durability and UV resistance to a lower carbon footprint and advanced hydrophobic performance”.
The recently launched range taps into the company’s “strong track record and experience in the development of innovative concretes that stretches back some 60 years”. AG’s Woodward Brick with Enduur comes in ten colours and both smooth (sharp) and antique (rumbled) textures. Woodward has been designed with a frog to improve buildability and stabilty, and this hollow depression also reduces environmental impact by saving on materials and reducing the weight of the brick, thus making it easier to handle.
Stephen Acheson, AG CEO, believes the new range is especially suited to Private Developers and Housing Associations. He said: “We know from our experience in these sectors that any product used needs to be aesthetically attractive and technically robust. Given the major growth being experienced in housebuilding throughout the UK and Ireland we believe Woodward is an attractive, durable option for those seeking a solution which ticks all the boxes and has less environmental impact than standard house bricks.”
Along with the majority of its products, the new brick is manufactured from locally sourced aggregates and graded to its precise requirements. The company uses a range of recycled materials including reclaimed materials from its own Washplant, and the manufacturing process is said to be much less energy intensive than that of traditional house bricks — the facing bricks cure naturally due to their inherent properties through an exothermic reaction and have no need to be baked in kilns at over one thousand degrees 24/7.
Click the link to find out more about AG’s Woodward Brick options.
AG has invested in “state-of-the-art” T-Rex sustainable packaging at its Toome plant as part of its overall environmental strategy. The system, supplied by Kraft Curing Systems, uses 100% biodegradable pellets that are sprayed onto each product layer for added surface protection before the next layer is added on top, without compromising on the quality of the finished goods.
The system replaces the customary foam layers which are traditionally set between layers to protect the product whilst in transit. Such foam layers are disposed of by contractors on site, but the T-Rex packaging system uses granules which biodegrade naturally in-situ, removing the need for disposal.
The company says the packaging system investment allows it to deliver on product requirements through a more efficient and sustainable method, further reducing carbon emissions through drastically reducing the amount of packaging in their products. The system is the latest in a series of sustainability initiatives created by the firm which include switching to 100% renewable energy as well as utilising bio-LPG instead of the industry-standard LPG, resulting in a carbon saving of 70%.
Last year, the business also reduced its Scope 1 and 2 emissions by 10%, despite a 30% increase in production volumes as the company faced unprecedented demand for its products reinforcing its commitment to a greener future in construction.