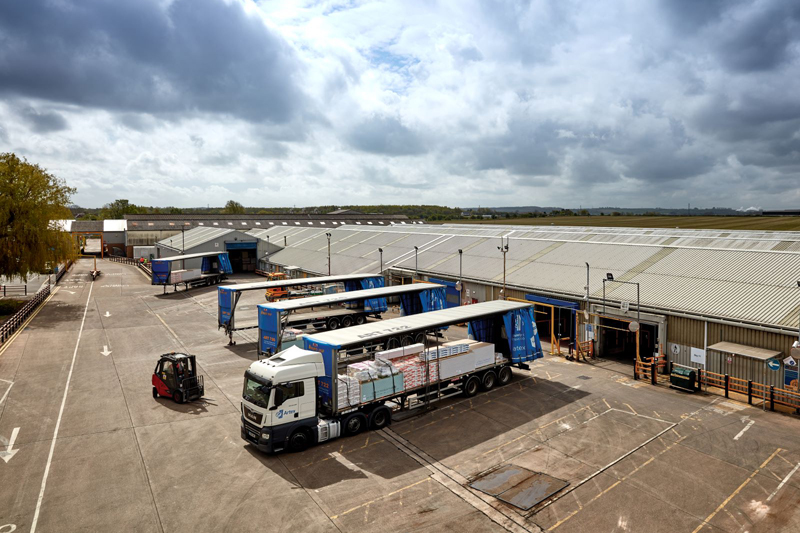
Alongside its fellow Saint-Gobain Group brands, Artex is implementing a number of initiatives designed to lessen its environmental footprint. PBM takes a look at the distributor’s focus on sustainability, and how it aims to demonstrate the importance of lowering carbon emissions throughout the construction sector supply chain.
As a well-known distributor of familiar construction product brands including Gyproc, Weber and Thistle Plasters, there’s a lot more to the Artex name nowadays than textured finishes. With a diverse portfolio and a long-standing heritage, the company says it can tailor its offering to match the needs of its merchant customers throughout the country.
Its support package for merchants includes an array of point of sale and marketing materials, whilst a flexible delivery service means that customers can order from as little as a single pallet — whether a full pallet of a single product, or a mixed pallet from across the range — and its Gyproc Express parcel service is said to ensure that smaller consignments can be rapidly despatched as required.
Beyond its product offer and capacity to deliver stock into merchant branches, the company is also placing an increased emphasis on addressing its environmental impact. Indeed, with the issue of sustainability rising up the agenda and the need for the construction sector — which is said to account for 40% of energy consumption in industrialised countries — to play its part, it is a responsibility the Saint-Gobain Group as a whole takes seriously as it seeks to address “the challenges of sustainable construction, resource efficiency and the fight against climate change”.
“In July, Artex also took delivery of a new Mercedes lorry which runs on ‘hydrotreated vegetable oil’ (HVO). The fuel is manufactured from sustainable, renewable feed-stocks and the distributor is now trialling the vehicle with the expectation of seeing a “90% reduction in CO2 when compared with its diesel equivalents”.”
The Group reports that it is in the process of finalising its zero-carbon roadmap which will set out a path for each of its businesses to meet medium-term Science Based Targets for 2030, with the ultimate goal of net zero carbon by 2050. This philosophy, which it summarises as a commitment to “make the world a better home”, encompasses all aspects of its activities, from developing new product solutions to implementing greater environmental efficiencies across its business and brands — from the buildings and operations, to its packaging and logistics.
For Artex in particular, the business has embarked on a number of recent initiatives — both larger and smaller scale — as it searches for ways to become a more sustainable organisation. For example, it was one of three Saint-Gobain Group companies to receive a share of £650,000 as part of the Group’s INVEST Carbon fund to support the decarbonisation of its businesses on their net zero journey.
Through the funding, the Wishaw branch of Jewson installed high performing insulation, LED lighting, solar photovoltaics and an air source heat pump whilst four branches of Jewson Civils Frazer are to replace their electric heating systems with air source heat pumps with the aim of saving 56 tonnes of CO2 a year.
However the biggest tranche, and one which is set to deliver the most significant result, was the £300,000 secured by Artex to fund the installation of a biomass heating system at its base in Ruddington, Nottinghamshire. Completely replacing and decarbonising the site’s existing heating system, it is estimated the project will reduce CO2 emissions by 150 tonnes a year — the equivalent to nearly 600,000 miles in a diesel car.
In July, Artex also took delivery of a new Mercedes lorry which runs on ‘hydrotreated vegetable oil’ (HVO). The fuel is manufactured from sustainable, renewable feed-stocks and the distributor is now trialling the vehicle with the expectation of seeing a “90% reduction in CO2 when compared with its diesel equivalents”. A 10,000 litre HVO tank has been installed in Ruddington and the trial will encompass the journeys where routes start and end at Artex, with the performances reviewed weekly to monitor the ‘real time effect’.
The business had already been using biofilm as pallet wrap, saving 12.5 tonnes of CO2 in 2020, and a plastic-use reduction of 3.9 tonnes. For its Gyproc Express parcel service, it uses eco-friendly boxes and has a tree planting programme for the boxes used — offsetting a further 49 tonnes of CO2 — whilst a review of its wider product packaging is ongoing.
With its Environmental Management System certified to ISO14001:2015, numerous other initiatives — from waste minimisation, cardboard and pallet recycling to the upcycling of old lockers into planters — are also in place on site, with many ideas put into practice following engagement with the firm’s employees.
As the importance of sustainable solutions gains further recognition within the sector, Artex states it is “making good progress” on its own journey to achieving greater carbon efficiency, acting as a responsible partner to help reduce the environmental impact throughout the wider supply chain.
For more information, visit www.artexltd.com/stockist-support