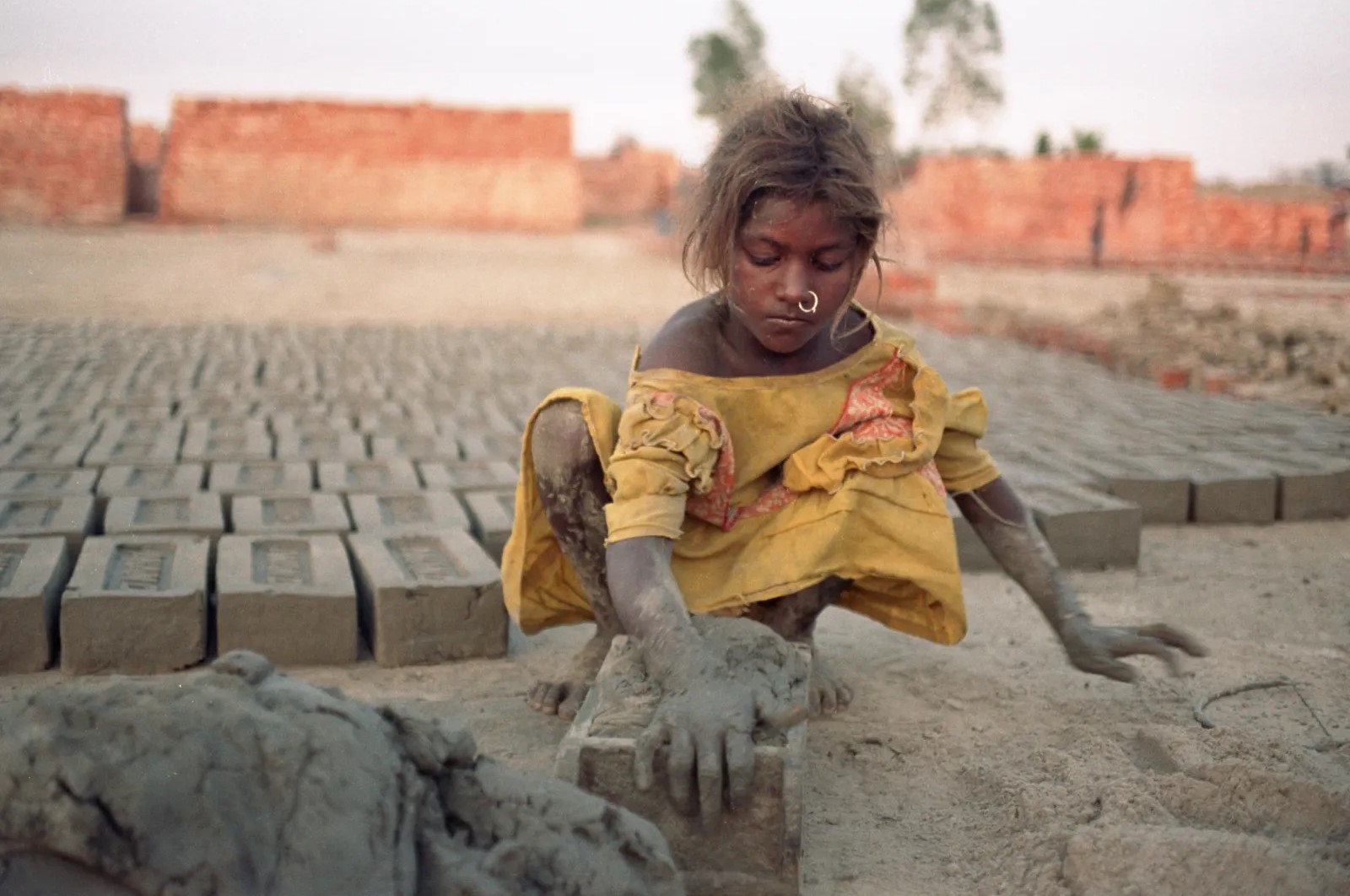
Asserting that it is “absolutely crucial to be aware of the provenance of clay bricks which are being sold in the UK,” the Brick Development Association (BDA) is running a hard-hitting campaign urging brick factors, brick buying groups and builders’ merchants to look “extremely closely” at the countries of origin of the bricks they sell.
“It is one of the manufacturing scandals of our time that clay bricks with dubious provenances are being sold freely and openly on the UK market,” commented BDA Chief Executive Keith Aldis. “If people realised the horrendous circumstances in which many of these bricks were being made, I’m sure they’d think twice before buying and selling them.
“This is why we have launched our pioneering Brickmakers Quality Charter (BQC), a benchmark for quality, responsible, ethical and sustainable brickmaking. The BQC is a response to the widespread fears about the way bricks are manufactured in some Asian countries, combined with the lack of longevity and sustainability of imported bricks.”
He continued: “In an ideal world, all brick factors, brick buying groups and builders’ merchants would check to see that the bricks they were selling had been manufactured by brickmakers who had signed our charter. It is disturbing that many importers, shipping into the UK, are not certified.
“There are many issues which need to be addressed concerning the importing of clay bricks. They fall short of decent standards on too many levels, including longevity, quality, sustainability, transport costs and carbon reduction, not to mention the fears around modern slavery and illegal deforestation, transport costs and quality issues we have with imports.”
“It is especially distressing to report that the scourge of modern slavery remains a stain on the global clay brick industry.”
Keith added: “It is especially distressing to report that the scourge of modern slavery remains a stain on the global clay brick industry. Through our forensic monitoring of statistics within the UK brick market, we had sadly discovered a significant increase in the importation of clay bricks from outside of the European Union into this country.”
According to the BDA, there is a “large defined area across Pakistan, India, Nepal and Bangladesh, as well as Sub-Saharan Africa and the Far East” which is causing great concern. These are places where bricks are manufactured seasonally, in large numbers, and — more often than not — using bonded or child labour.
Keith said: “It is clear that those unfortunate people who are making these bricks work under extreme conditions with little or no regard to health and safety. The sanitation and the pay are dreadful and sometimes non-existent. This is unacceptable in today’s business world — which is why we are encouraging all responsible brickmakers to sign up our ground-breaking The Brickmakers Quality Charter, which is designed to put a stop to modern slavery within the brick industry.”
Mr Aldis was especially critical of suppliers who simply re-brand poor quality bricks “with heart-warming British-sounding names in order to associate themselves with the good reputation of UK clay brick and the potentially lucrative UK clay brick market.”
In a rallying cry to brick factors, buyers and builders’ merchants, Keith urged: “Please, please don’t buy and sell brick with dubious provenances. You will be aware of where these bricks have come from and the best way to stamp out modern slavery is not to deal with companies who manufacture bricks in intolerable circumstances.”
He stressed that a buyer always needed to ask a supplier or manufacturer where the bricks were made and if anyone was ever in doubt, simply ask if you can visit the factory. Any reputable manufacturer would be delighted to host you and show you around.
Keith concluded by saying: “If the clay brick or paver is manufactured in the UK (or in the EU), then you can be certain that it is manufactured to correct standards and to a suitable consistent quality. Our Brickmakers Quality Charter, promoting the responsible sourcing of clay brick, makes this process of checking so much easier.”
Guy Armitage, MD of the award-winning BDA member York Handmade Brick, explained why his company signed up to the charter shortly after it was launched. He said: “We are very proud to have been honoured for our high ethical standards — as the brick industry fights back against the widespread use of child labour and slavery in South East Asia. We take huge pride, both in our environmentally friendly brick-making process and in the way we treat our loyal and hard-working staff.
“Sadly, this approach is not shared by some of our competitors, who encourage their customers to unwittingly buying cheap and unethically produced imported bricks, made to lower standards, but passing themselves off as made to the same standards with nothing but slick marketing for certification. This is unacceptable on a number of levels, the worst being the use of bonded and child labour to make these bricks. This is exploitation on a terrible scale and is a stain on our industry. The excellent Brickmakers Quality Charter scheme is the first, and very significant, step in trying to stamp this out.”
Click or tap the link for more information about the BDA’s Brickmakers Quality Charter and to view approved firms.
A version of this article appeared in the February 2024 edition of Professional Builders Merchant. Click here to view the digital version of the issue, via the PBM website.
With one element of the Brickmakers Quality Charter asserting the sustainability aspects of locally sourced bricks, BDA CEO Keith Aldis is keen to stress the ways in which the UK’s brick manufacturing sector is spearheading efforts and striving for net zero carbon emissions, focusing on the eco-friendly attributes of bricks.
Bricks are natural, durable and easily maintained, providing benefits throughout their lifecycle. However, despite their inherent sustainable characteristics, the UK’s leading brickmakers recognise the challenges posed by carbon emissions and the need to overhaul the manufacturing process to this end.
Keith cites the example of BDA member Forterra’s recent £95m investment in a new super plant at its Desford site in Leicestershire, which will be capable of producing 180m bricks per year while significantly reducing the carbon impact of each brick manufactured on the site compared to its previous factory. Similarly, Ibstock aims to create the world’s first Net Zero brick factory for Scope 1 and 2 emissions.
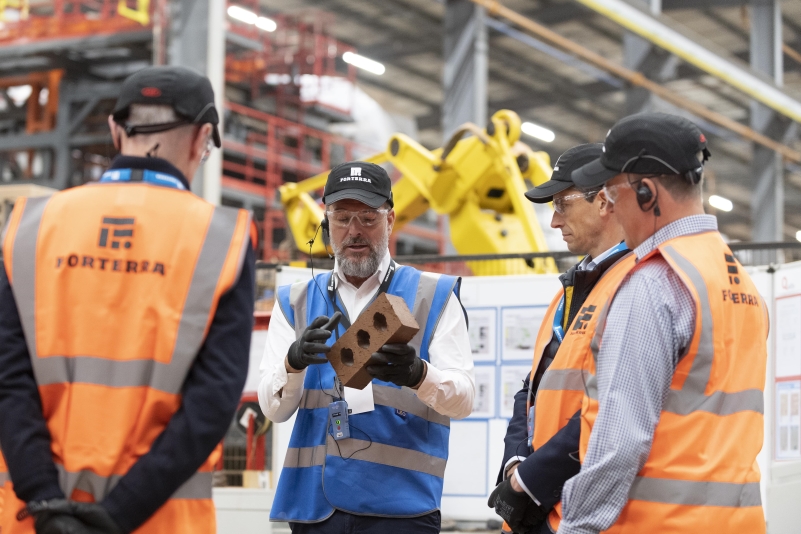