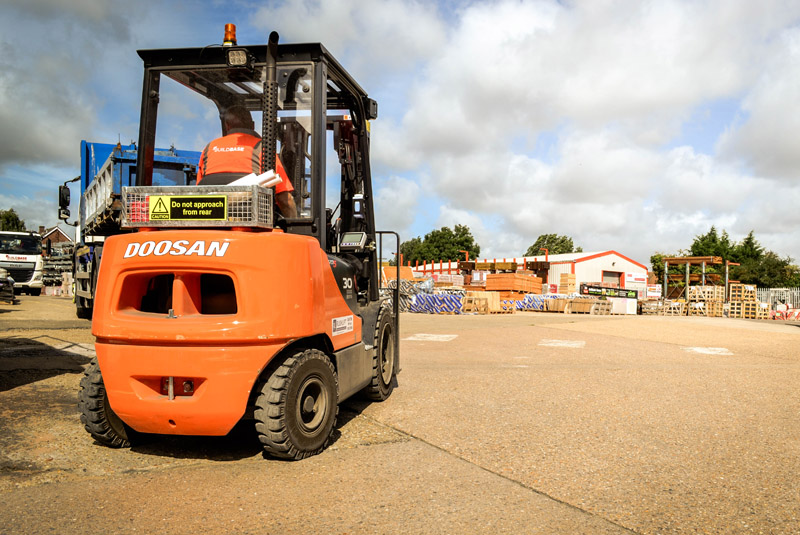
With more than 165 branches nationwide, excellence in customer service, with high product availability and fast delivery, is a corner stone of the Buildbase business strategy. In the merchant sector that means having the mechanical muscle to handle the heavy materials and products traded on a daily basis.
“We need good, reliable, robust forklift trucks with fast service back-up,” says Fraser Boyd, Transport Operations Manager at Buildbase. Over the last two years, the building supplies company has expanded its service support for its forklift truck fleet through Rushlift, a UK subsidiary of Doosan Industrial Vehicles.
“Ensuring the uptime of our forklift trucks is absolutely essential to the efficient running of our sites. So having reliable and fast service back-up and support, across all our sites, requires a service organisation that can provide nationwide coverage – even to really outlying areas such as the Highlands and the Shetland Islands,” he says. “Rushlift accommodate all our service requirements. They outsource some services in the most far-reaching areas, but importantly, they are able to facilitate this for us, giving us just one point of contact. With any breakdowns or servicing needs they just make it happen, which takes a big burden off of our shoulders.”
The relationship with Rushlift and Doosan has grown steadily and in 2016 an order was placed for 30 new Doosan 3 tonne and 3.3 tonne diesel powered counterbalance trucks for several Buildbase sites. The standard D30S-5 and D33S-5 Doosan models offered the tough, ‘no frills’ capability the merchant was looking for. “We wanted a robust piece of kit that is easy to maintain – nothing too complicated or full of electronics that are going to keep breaking down every few days,” adds Fraser.
Doosan’s standard ‘feature-rich’ models include the oil-cooled disc brake system – perfect for the dust and grit of builders’ merchants’ yards. Manufactured as completely sealed units the system is protected against outside elements, such as water, dust, dirt, shrink wrap and metal banding – ensuring top-rate braking performance, for enhanced safety and increased productivity.
This low-maintenance, heavy-duty braking system provides increased uptime and reduced running costs when compared with conventional shoe or drum brakes, says the company.
In addition to the standard specification, the trucks supplied to Buildbase were fitted with front, overhead and rear screens, speed limiters for safety, rear grip handles for driver comfort when reversing, a rear mounted tool tray, steel under panels for extra protection on rough ground, and on the 3.3 tonne models, brick clamps for palletless handling and loading.
“We trialled competing brands at our Nottingham and Leicester branches for a couple of weeks and the feedback on the Doosan trucks was really positive,” continues Fraser. “The drivers liked the smooth operation of the levers and the ease of raising and lowering the forks. And the Doosan trucks scored highly on driver comfort, stability, safety and visibility through the forks too – which were all important points for us.”
Parts back up also played a significant role in securing the deal. “The Doosan parts centre in Northampton really made an impression. They keep a good stock of spares and they can dispatch overnight for parts delivery within 24hrs, which offers great security. No one else seemed to want to talk about parts, but Rushlift showed us exactly how the centre works.”
One additional benefit of choosing Rushlift was the capability to supply and support Bobcat tele-handlers, which are also owned and manufactured by Doosan, as well as specialist products manufactured by Combilift.
Overall, it was the designed-in serviceability of the Doosan product, its on-site performance and the lifetime cost of the truck that counted. Fraser concludes: “Compared to other manufacturers, we’ve seen that the whole-life servicing costs could be significantly reduced due to the way the Doosan truck has been engineered and designed. The whole package was there for us – and with the backing of Rushlift’s nationwide servicing, it ticked all the boxes.”