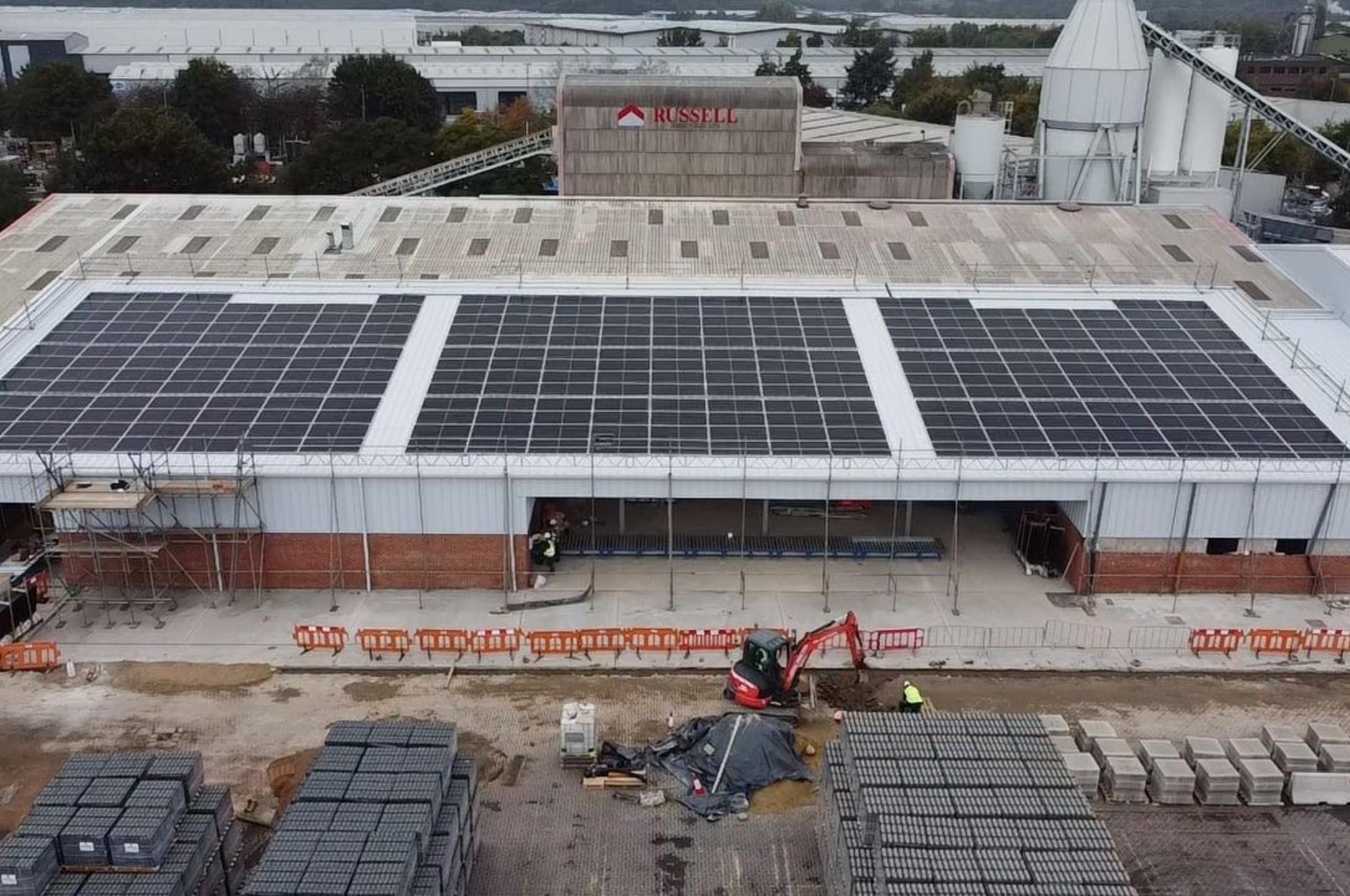
Russell Roof Tiles has continued to take steps to reduce its carbon footprint with the installation of solar panels at its new £18.5m upgraded plant.
The overall investment, which is the concrete roof tile manufacturer’s largest to date, began last year and will double the manufacturing output at the nine-acre site on Nicolson Way in Burton-on-Trent. Across the whole operation, the supplier has been actively seeking ways to reduce its environmental impact, including investing in more energy-efficient equipment, optimising production and sourcing more sustainable materials.
As part of this, 165kW of solar panels and four Solis inverters have been installed to help power the new production facility. UK renewable services provider Alt-Group installed the system in a matter of days, enabling the manufacturer to reduce its carbon output.
This is the first time Russell Roof Tiles have installed solar panels on one of its factories and comes as the government’s reactivated “solar taskforce” names solar power as a driving force behind the UK’s 2030 clean power mission, a key step in meeting its 2050 Net Zero target. The manufacturer is currently on its own journey, pledging Net Zero Scope 1 & 2 emissions by 2040.
Daniel Hancox, Corporate Sustainability & Development Director at Russell Roof Tiles, said: “When we say we’re committed to reducing our carbon footprint, we mean it. A big thanks to the Alt-Group team who did a great job getting the panels up and running, one of many steps we’ve taken to reduce our carbon emissions. We’re at a crucial stage in this investment journey currently and it’s exciting to see everything coming together.”
Alongside the solar panel installation, the new plant will also feature sustainable benefits such as a water reclamation and refiltering system that allows for recycling of all wash water. This will reduce the firm’s use of fresh water, and significantly reduce waste.
In addition, the Nicolson Way investment will deliver more manufacturing lines within a new 1600 sq/m building using a 30-ton steel frame which houses a state-of-the-art curing chamber for its concrete tiles, which is a significant part of the new plant. Not only will the new facility produce a product that is of higher quality, strength, and consistency, but it will also speed up the drying process.
New “Triple Tile Innovation” designed to speed up roofing installation
With the new Government committed to delivering 1.5 million homes during this Parliament, speed of construction is going to be a priority. Accordingly, Russell Roof Tiles says its new Bute3 roof tile is the perfect solution as it is said to be 33% quicker to install than other thinner leading-edge interlocking tiles.
Reportedly the first of its kind in the UK, Bute3 is a triple interlocking multipurpose roof tile and its innovative design and colour options “provide the first real alternative to small-format concrete, natural clay, and slate roof coverings.”
The manufacturer has invested more than £2million and five years in design and development, “pushing the boundaries of concrete roof tile manufacturing.” The tile is being produced at its brand new, £18.5million fully automated production line in Burton on Trent – designed specifically for this product – with the company adding that such a tile “has never been made at high production speeds before, anywhere.”
Andrew Hayward, Managing Director at Russell Roof Tiles has led the development of the new product, working closely with design, manufacturing, and technical experts over the past five years. He said: “The market has grown consistently over the past 30 years for thinner concrete roof tiles, but quality and tile strength have always been a major challenge for manufacturers.
“But we have addressed this issue head-on, making this huge investment in designing Bute3, a tile that utilises all of the latest pioneering technology and precision engineering to create a multifunctional triple interlocking tile of the highest quality, which meets the demands of both planners and installers.
“We’re very excited to finally bring Bute3 to market, a high-quality product which matches the superior, design capabilities and production qualities reflected in every aspect of our current range.”
The all-new triple tile has the strength and characteristics of a regular large format tile and is being launched in six colour options, two of which (Terracotta and Burnt Orange) provide a “credible alternative” to popular clay interlocking and plain tile products on the market. In addition, Bute3’s triple-tile format allows for excellent coverage with only 10.9 tiles per square metre, significantly reducing the number of tiles needed compared to traditional plain tiles.
The product is also suitable for roofs with a pitch as low as 25°(22.5°site dependent), offering flexibility in application while maintaining strength and durability.
Bute3 gives the appearance of three concrete/clay plain tiles or small format slate when laid yet the product is based on a medium interlocking tile format. It also provides a comprehensive full roofing system that includes bespoke Dry Verge and Dry Fix Systems, in-line vents, and specialised tile clips, ensuring a secure and long-lasting roof.
Listening to market challenges, the firm says that the new product has also been designed to ensure there is no requirement for ancillary tiles as there is with ‘twin tiles’. This reduces the need for left and right hand ¾ verge tiles or tile and halves ensuring Bute3 is easier for estimating, tendering, and ordering.