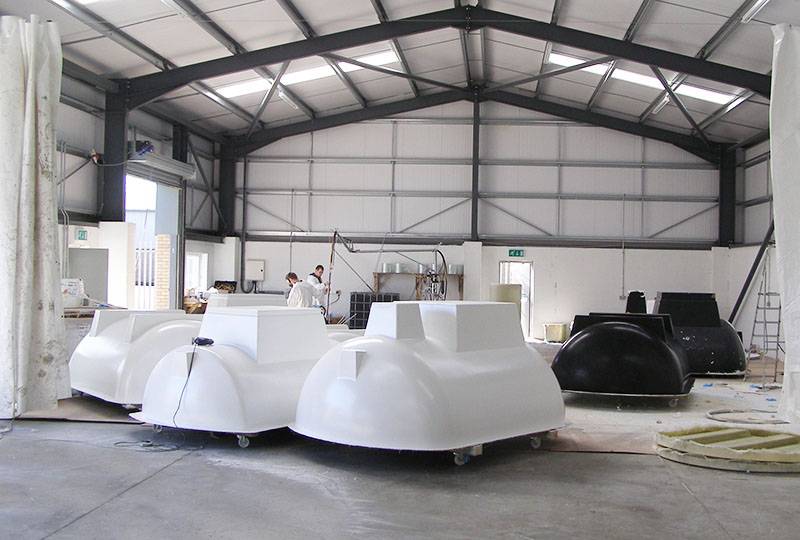
Marsh Industries is a privately-owned company specialising in advanced off mains drainage solutions for the domestic, commercial and agricultural wastewater treatment sectors. PBM reveals more.
Fact File Key Contact: Steve Boyer, Managing Director Head office: Units 2-16, Addington Park Industrial Estate, Little Addington, Kettering, Northants. NN14 4AS Tel: 01933 654582 Email: sales@marshindustries.co.uk Website: www.marshindustries.co.uk Product range: Off-mains drainage products for the domestic and commercial sectors. Accreditations: ISO 9001 Registered. All products fully type-tested and CE approved. Trade Associations: Members of BMF, NMBS, H&B, FORTIS and IBC. No of staff: 60+ Company comment: “Marsh Industries delivers world-class water/wastewater treatment products and solutions to the domestic, commercial and agricultural sectors from its UK manufacturing plants in Kettering, Bridgwater and Raunds. The company is recognised as a collaborative and trusted partner to its customers, with a reputation for providing quality products that really do add value.”
Operating from bases in Kettering, Raunds and Bridgwater, Marsh’s specialist engineering, technical, manufacturing and distribution teams have provided products to the construction market since 2006. From small 234 litre pump chambers to 500-person commercial sewage treatment plants, thousands of Marsh products are currently in use across the UK and Europe.
Products in the firm’s portfolio include sewage treatment plants, pump stations, septic tanks, septic conversion units, grease traps, oil separators, stormwater attenuation, rainwater harvesting systems and a host of ancillary products including the unique ‘Whisspurr’ acoustic vibration reduction unit.
A significant differentiator at Marsh is, as a privately-owned company, said to be the ability to invest in continuous research and product development programmes. The firm says that this capability ensures its products and solutions are at “the forefront of technology, are specified precisely and exceed the recommended UK or EU standards”.
Taking a proactive approach to the ever-changing environment of the industry and manufacturing, Marsh reports that it has identified “advantages that can be achieved by a research and development capability that expands the focus beyond the immediate expectations of customers and their requirements”.
This proactive approach, it says, has been established since the company’s inception and is still in practice today.
In 2009, when Marsh entered the commercial sewage treatment plant sector, the company performed a thorough assessment of the market with a focus on the demands and requirements of specifiers, engineers and end-users. The analysis of the market at that time proved there was appetite from merchants, specifiers and engineers alike to be more involved in sewage treatment plant design and system performance, with end-users showing a desire to understand plant maintenance.
The first major step for Marsh was to develop the Gaia Sége process design software in alliance with Loughborough University. The software uses established core equations to generate process optimisation for any size of commercial sewage treatment plant, providing assurance to specifiers, engineers and the end-user that the system is specifically designed to meet or, in most cases, exceed the needs of the site and satisfy the appropriate standards and regulatory bodies.
In addition, Gaia Sége can generate three unique tank size options in 1.8, 2.5 and 3m diameters allowing specifiers to choose which tank best suits the site conditions. These options are provided at no extra cost; each tank is the same price so that customers are never disadvantaged by their site conditions or layout.
Then next step was an alliance with Polylok Inc USA for the exclusive use of the Polylok Tertiary Filter in the UK. Pilot tests with WRc proved that a further 35% reduction in Suspended Solids and a reduction of Biological Oxygen Demand could be achieved post treatment within plants, meaning that the effluent discharge from the sewage treatment plant exceeded the most stringent UK and EU standards, and is almost safe enough to drink (although not recommended!).
The Marsh Ultra:Polylok commercial sewage treatment plant was brought to market in 2016 and the firm says it was welcomed by merchants, specifiers and end-users alike. Since its launch, additional features such as carbon vented manholes and turret safety guards were added as standard to the range, further enhancing the system and making it what the company describes as being the “safest, most advanced commercial sewage treatment plant on the market”.
Now in 2020, Marsh has launched an eco-friendly processing solution to accompany its range of Ultra:Polylok sewage treatment plants.
Managing Director, Steve Boyer, explains: “Once again, the company’s research and development programme identified concerns from end-users regarding energy consumption and high running costs due to continuous plant processing or, in worse case scenarios, incorrectly sized sewage treatment plants.
“The Marsh eco-friendly processing system offers the ability to control sewage processing conditions for any site. This allows end-users to further optimise processing during high periods of loading whilst returning to lower levels during quieter periods, meaning reduced energy consumption and overall improved running costs.”
He concluded: “We are all proudly committed to our policy of continuous innovation and improvement across our full range of products and services. This policy encourages the team and instils a confidence in our products that is unrivalled in today’s marketplace.”
For advice on any off-mains drainage project, click here: https://marshindustries.co.uk/marsh-industries/