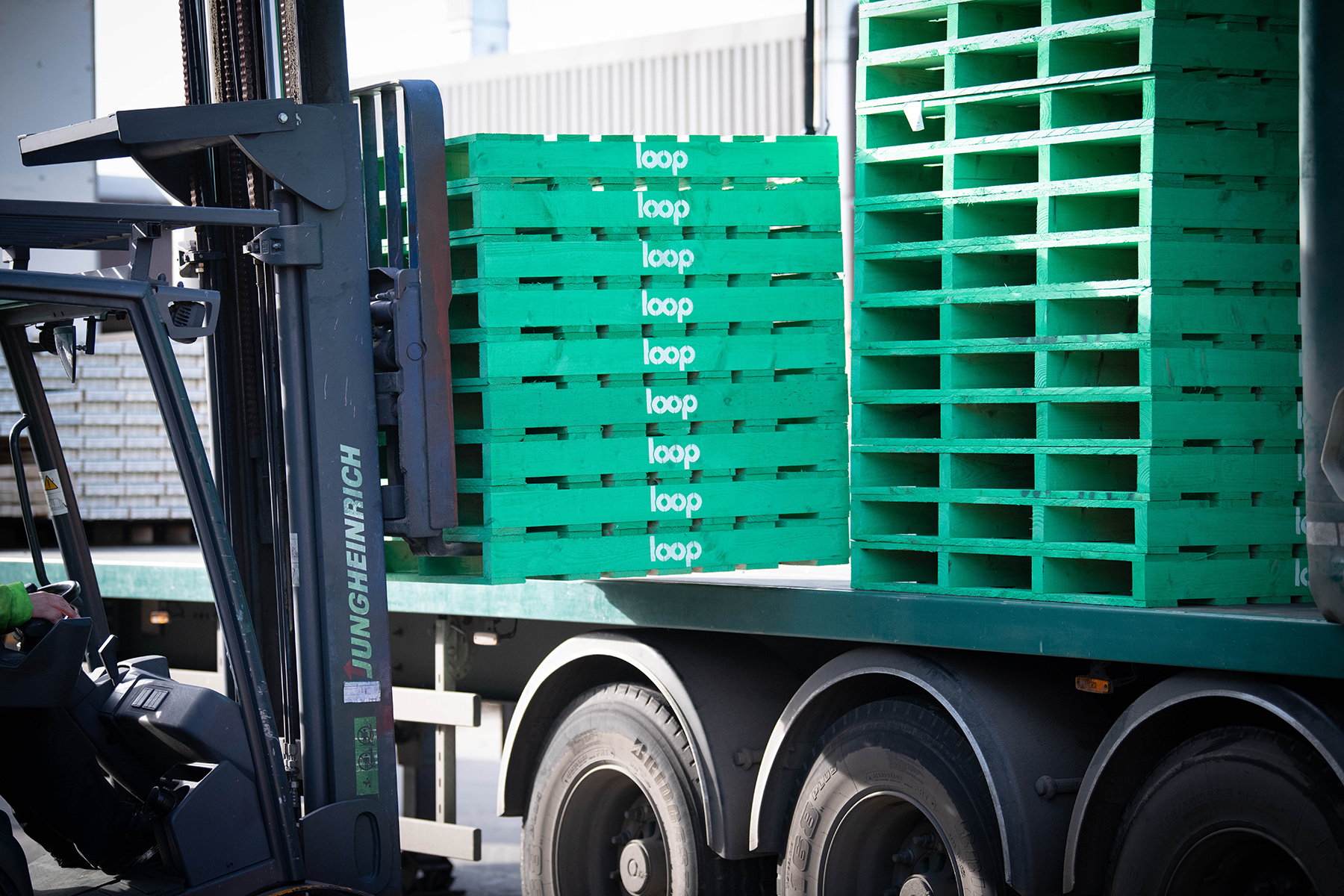
In partnership with British Gypsum, the latest phase of The Pallet LOOP scheme has just seen the introduction of a second specification of its distinctive, green-coloured reusable pallets for transporting the manufacturer’s plasterboard products. PBM speaks with LOOP founder and CEO Paul Lewis to discuss the background to this game-changing sustainability initiative for the construction sector.
Go to almost any merchant yard, visit any manufacturer’s production facilities or take a look at building sites large and small up and down the country and you’ll be confronted with an issue so common that, paradoxically, it almost goes unnoticed: ubiquitous yet effectively unseen stacks of discarded single-use pallets, accepted almost as an occupational hazard and all-too-often, just waiting to be thrown in a skip.
“The industry has been stepping over pallets for years,” Paul Lewis, founder and CEO of The Pallet LOOP, succinctly explains, highlighting a problem that has become “accepted… as just the way things are done in construction.”
With first-hand knowledge of the sector from working for his family’s pallet producing business, HLC (Wood Products) Ltd, Paul states that more than 20 million pallets are manufactured and distributed throughout the UK construction industry every year. To create these pallets, an estimated 6,000 acres of forestry are harvested annually with a further 236,000 acres grown to cater for future demand.
However, less than 10% are reused as producers typically only recover around 5% of pallets, meaning that the vast majority are scrapped after just one use. And even though most pallets circulating within the sector are cost engineered to be single use, the net effect is to add unnecessary waste at significant expense to the supply chain — not least for those having to manage the disposal process.
In an era of increased environmental consciousness reinforced by increasingly stringent legislative measures, the disposable nature of current pallet production is inefficient, costly and can no longer be considered sustainable — in any sense of the word.
However, Paul’s experience of supplying into the FMCG retail sector — where far greater numbers of pallets “flow and return” throughout the supply chain and reuse is typically around 98% — presented the potential for the industry to accept and adopt a better model.
The family firm was sold to The Scott Group in 2019 and post-exit, Paul channelled his passion for pallets into creating a new distribution model with the foundation of The Pallet LOOP. Built around the concept of the ‘circular economy’, the business aims to provide construction companies with a “greener, leaner and more cost-effective way of transporting building materials” by moving away from the current pallet practice of ‘deliver, distribute and discard’ to the principles of ‘recover, repair, reuse’
Designed for reuse
Its durable, green pallets are specifically designed to be reused, and The Pallet LOOP has a dedicated recovery infrastructure in place — enabled through its partnership with Scott Pallets — to ensure they can be returned to suppliers and re-enter circulation. The concept has been continuously reappraised ahead of launch, moving away from an initial ‘deposit scheme’ to one that actually incentivises returns through an easy-to-administer collection system that pays up to £4 for every pallet registered return partners (such as merchants) ‘put back in the LOOP.’
From the outset, Paul recognised the importance of engaging with industry stakeholders and the business has worked to build its profile. Joining the BMF as a Service Member, it won the Federation’s Sustainability Award in 2022, and embarked on a series of working groups with BMF members to outline and refine the concept.
Numerous manufacturers, merchants and construction firms signed up to an initial ‘charter’ acknowledging that “change is required” when it comes to pallet consumption, and the business has also forged relationships with the likes of NMBS and other merchant buying groups such as IBC, NBG and Fortis.
The team has expanded, including the appointment of well-known industry figure Andy Williamson as Director of Business Development in February this year, to deliver the required buy-in and volume for the system to work. Partnering with manufacturers remained paramount to get the pallets ‘into the system’ and the real breakthrough came earlier this year when an agreement with manufacturing giant British Gypsum came on stream.
The rollout began in early May with the despatch of the returnable, green-coloured pallets for the supplier’s bagged plaster ranges, and the latest step sees British Gypsum using a second specification — a 2400 x 1200mm two-way entry pallet — for the distribution of its plasterboard materials.
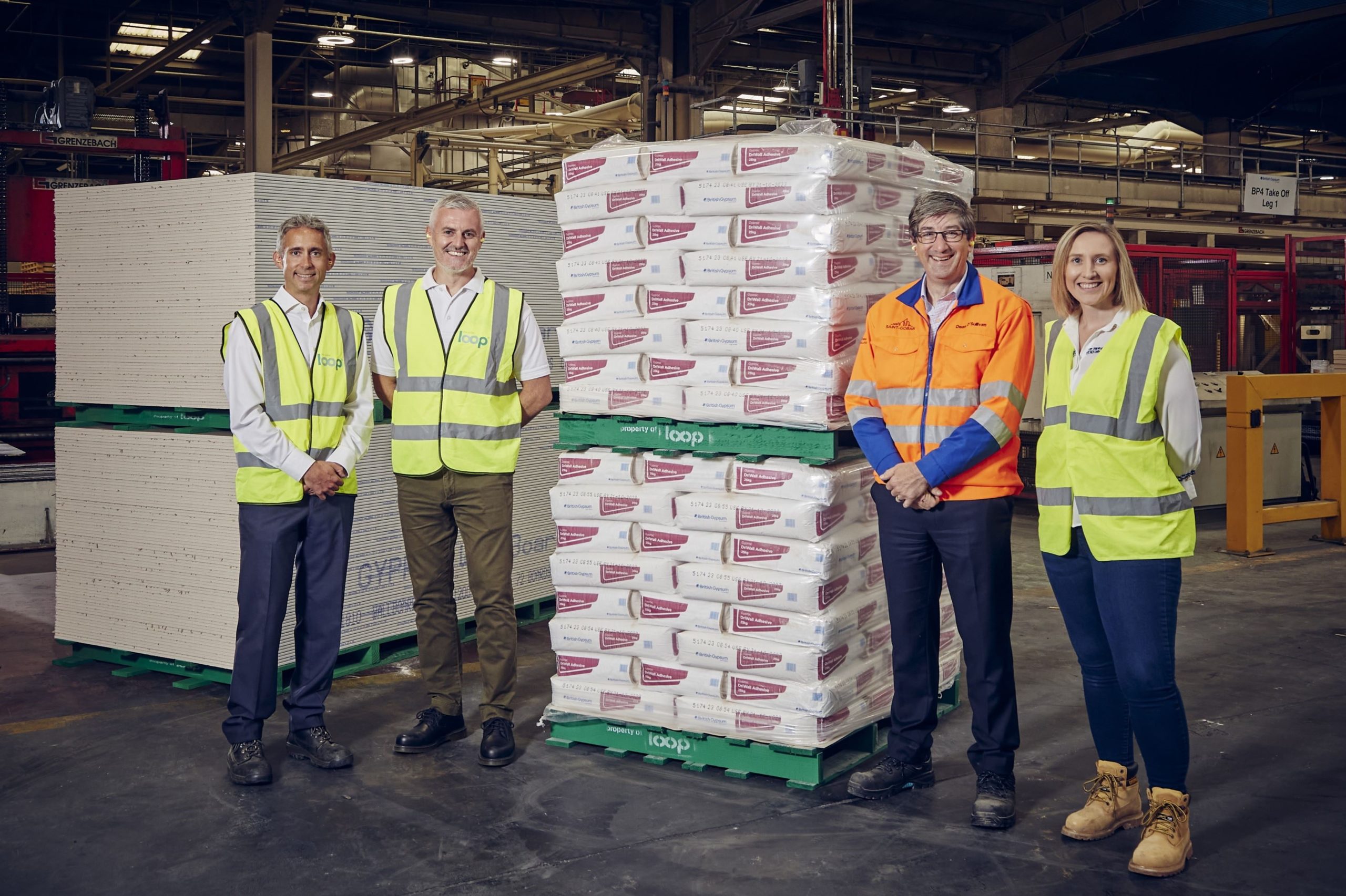
In what is ultimately intended to see more than 1.6 million of the circular economy pallets across UK construction, more than 40,000 of LOOP’s plasterboard pallets were shipped out in July to be processed through British Gypsum’s Sherburn, East Leake, Kirkby Thore and Robertsbridge plants and — once loaded with product — sent into the market.
Steve Ottaway, the scheme’s Head of Operations, said: “Twelve weeks in and The Pallet LOOP is now starting to really motor along. With the number of green pallets in the market increasing by around 20,000, week on week, we’re already starting to see pallets coming back from distribution centres, merchants and principal contractors nationwide.
“At this early stage, we’ve already been able to put around 3,000 LOOP pallets back through the supply chain, for the second time — a first step towards pallet circularity that will have a positive impact on the sector’s carbon, timber usage and waste numbers.”
Steve added: “We look forward to the number of returned pallets growing significantly over the coming months — to ultimately go back into the LOOP. In the meantime, our message to businesses that receive pallets, en masse, is simple. When you get green LOOP pallets, don’t put them in a skip. Stack them up and get in touch.
“We’ll get you signed up for collections, come and take away any pallets you have and give you money back. We can also pick up white pallets too.”
For the final words, we return to Pallet LOOP founder Paul Lewis. Positing on LinkedIn on 29th May once the firm’s distinctive pallets entered the UK construction supply chain, Paul wrote: “The feelings that come with seeing our vision become a reality are overwhelming. From an idea back in 2017, and subsequent business formation in 2019, over the last five years, the team and I have worked diligently, with determination and resilience, to get this project over the line and deliver a world first in construction.
“It’s not been easy, but we’ve always kept our end goal in mind — to deliver a service to help UK construction minimise avoidable pallet waste. With discussions ongoing with other material manufacturers that wish to transition to LOOP, this is the beginning of a major shift in the way building materials move, which is better for business, and the planet.”
Click here for more information on The Pallet LOOP.
The business has also launched a series of short videos outlining the scheme and how to set up the collections and payback process. See below: