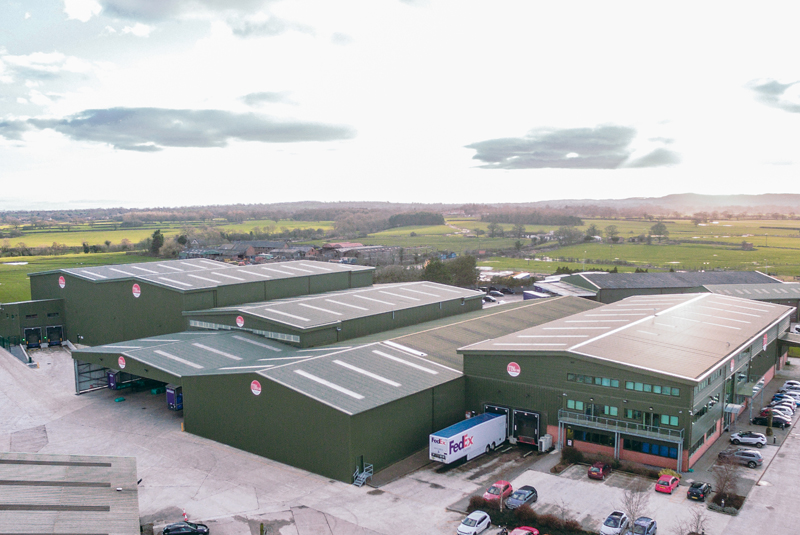
TIMco has extended its UK quality control facilities to meet the requirements of its growing product base and provide customers with product training and testing facilities.
The QC facilities are part of TIMco’s latest investment in a new 30,000sqft warehouse space which has been implemented to provide further quality control checks on products when they arrive in the UK.
The company already has QC facilities in its offices in the Far East that monitor the manufacturing process and ensure no products are dispatched to the UK without effective checks. On arrival to TIMco’s Cheshire offices, products receive further testing before they are stored and distributed to customers.
The new facilities will include a range of technologies from salt spray test machines to devices that measure load and insertion speeds. Products that fail the tests at any stage will be removed from the supply chain, while products that pass the tests will be verified for use.
The facilities will also provide customers with the opportunity to visit TIMco’s offices to learn how products work and their best applications.
Simon Midwood, Managing Director of TIMco, commented: “We’re committed to providing a broad range of high quality products to our customers and testing them effectively is a key part of delivering on our promises. The new state-of-the-art facilities ensure that our standards remain high and also provide us with an opportunity to train customers on our latest products and their applications, which in turn improves their product knowledge and benefits end users. We strongly advise that customers utilise these facilities and services which we can offer.”