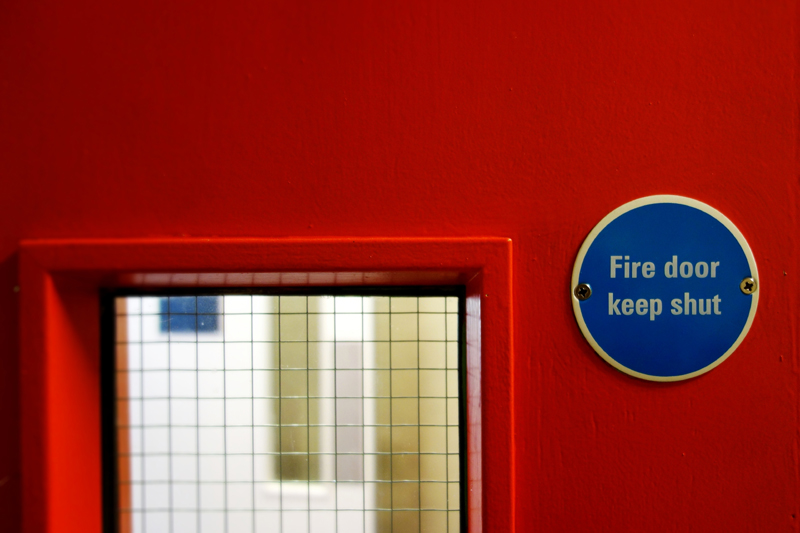
Fire doors are a vital component of any fire safety strategy and when designed, tested, manufactured, installed and maintained correctly, they can help to save lives. Much greater attention is being placed on this when properties are built, maintained and upgraded, which has seen the roll out of new regulations in recent years, bringing fire door compliance into sharper focus. Following the publication of its new white paper on the subject, JELD-WEN explores the implications.
The renewed focus on fire door performance began with the introduction of the Fire Safety Act 2021 in May 2022, which modified the previous Fire Safety Order (FSO) to clarify several points for those involved in assessing and insuring fire safety risks. Even more recently, Fire Safety (England) Regulations 2022 came into force on 23 January 2023, following recommendations to the Government in the Grenfell Tower Inquiry.
In certain cases, a building safety manager will also be required to oversee fire door specification, fitting and maintenance, whilst ensuring residents understand the importance of fire door safety. However, whilst the requirement is for a ‘Responsible Person’ to undertake best endeavour annual checks of flat entrance doors, and quarterly checks of communal doors in multioccupancy residential buildings above 11m, merchants might find themselves being a front-line source of expertise, information and advice for these individuals, and for customers looking to achieve better fire door safety.
By working closely with manufacturers, merchants should ensure they understand the impact of these regulations and, most importantly, which products — including hardware and doorsets — are best suited to different conditions and building requirements to provide maximum fire protection.
Shutting the door on risk
Whether they are carrying out a new installation or refit, it is crucial that customers choose the correct components for complete fire door assembly — particularly as the most common fire door failures include damaged seals, excessive gaps, and faulty, loose or unsuitable hinges.
Everything from the door material to its size, weight and functional performance can make a difference to hardware requirements, but for many purchasers, the deciding factor can often come down to cost savings. However, the reality is that failing to buy compatible components can compromise risk by inhibiting the performance of a fire door.
Although a Responsible Person should be capable of inspecting fire doors to identify any obvious issues, there is currently no stipulation for formal training or qualifications when it comes to installation. Fire doors are a specialist item, designed to create a line of defence and compartmentalise a fire break out.
Installing them is not only a critical safety task, but also a complex one, and a lack of competence or the smallest of errors during fitting can render the door not fit for purpose.
To help with this, each fire door should come with its own manufacturer installation instructions and certification data sheet, which sets out the exacting requirements of every component needed to ensure compliance. Although addressing these detailed technical requirements may be a standard process for experienced fire door installers, the wide range of variables involved can pose a significant challenge for non-specialists.
Fit for purpose
To ensure customers have access to the most appropriate product, merchants should endeavour to stock all fire door assembly items from manufacturers that carry a third-party UKAS-approved certification, demonstrating that their products are compliant and fit for purpose. This involves the manufacturer committing to rigorous testing with considerable investment in time and money, and provides the end user with consistent and high-quality fire protection.
For example, accreditation like the BWF-CERTIFIRE Fire Door and Doorset Scheme will subject manufacturers to UKAS-approved testing to BS476 part 22 or EN 1634-1, every five years, or for every 250,000 doors produced; an annual third-party audit; regular training of the latest Building Regulations; and an assessment of the ISO 9001: 2008 quality management system.
A golden opportunity
Following recommendations from the Grenfell Inquiry, the government continues to point towards a ‘golden thread’ as a tool to improve safety management. Requiring a readily-available digital trail of products and procedures that contribute towards fire and structural safety, a golden thread applies throughout a building’s lifecycle — from design to occupation and ongoing management — aiming to keep its occupants safe.
With fire doors, this should extend beyond the traceability afforded by certification processes, to include specification, installation, management and maintenance details. If it becomes standard practice, the golden thread approach may achieve greater transparency and accountability, enabling stakeholders to trace the origin of a problem and take corrective action quickly.
Throughout the supply and distribution chain, each party has an important role to play in minimising risk. The expertise offered by merchants can be invaluable for contractors and building safety managers, who may have limited time and resources to understand the significance of what may be perceived as relatively minor purchase choices, and getting to grips with the evolving fire safety landscape.
By taking the time to review product specifications and keeping informed of best practices, merchants can have an important role to play in opening the door to a new era of fire safety for all.
Click the link to download JELD-WEN’s white paper ‘Fire Safety: Time to Shut the Door on Risk’.
A version of this article appeared in the February edition of Professional Builders Merchant. Click here to read the full digital issue via the PBM website.