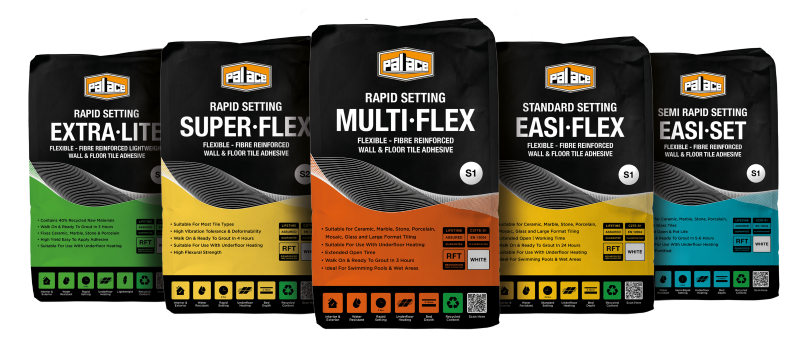
Having marked its 45th anniversary last year, Palace Chemicals has announced it is rolling-out a “brand rejuvenation” over the next few months, starting initially with its tiling products.
The Speke-based firm, reportedly one of the UK’s largest independent manufacturers of tile adhesives, grouts, building chemicals, wood treatments and decorating sundries, states that the move is a celebration that reflects its leading position in the tiling, flooring and DIY markets. Furthermore, the changes are intended to unify the growing family of Palace’s acquisitions over the years, including brands such as Langlow, Houseplan and, most recently, Rock-Tite, Pro Gyp-Base & NX.
The British manufacturer is also aiming to “cement its reputation as a trusted leader in sustainable manufacturing and remind the market of its continued drive to supply cutting-edge product advancements.”
Commercial Director Steve Ball said: “We not only have a broader product range than any of our UK competitors, but we lead the way in sustainable manufacturing, thus earning our status as a highly trusted supplier and pride ourselves on providing customer service that is second-to-none. This is what 45 years of trading has achieved – yet we refuse to rest on our laurels. This anniversary, combined with our refresh, is as much a celebration of where we are heading in the future as it is about our past.
“We’re most definitely in our prime, and we have no plans to take our foot off the gas in terms of bringing continual improvements to our products and production processes.”
Indeed, the company says that key to its success and reputation is its pursuit of ever more sustainable production methods. Palace was the first company in the sector to be awarded BS5750 (later upgraded to ISO9001) whist in 2004 it became an ISO 14001 manufacturer for its Environmental Management System. It was accredited by the BSI for its BS OHSAS 18001 Health & Safety Management System in 2014, which was then updated to ISO 45001 in 2018.
Further investment has led to zero waste to landfill produced during Palace Chemicals’ operating processes. Production is integrated with a closed-loop dust extraction and recycling system, which ensures all airborne dust emissions are contained and collected within a network of extraction ducting around all powder manufacturing and packing processes on site.
In addition, the business states that it is continuing in its mission to remove plastics and non-recyclable packaging from its system where possible. All of its plastic-based packaging, for example, now contains a minimum of 30% recycled and recyclable plastics.
Technical Director Jim Percival added: “Sustainable production is one of our most important achievements, and our current system represents a huge step forward compared with previously available technologies.
“It is a unique example of how investment in sustainable technology can have tangible and long-lasting benefits.”
Sustainability is also said to follow through in the company’s impressive record of staff retention. Many employees have loyally stayed with the company for several decades, which the business believes not only reflects its stature as an “exemplary employer” but also highlights value customers place on long-term relationships.
Having started originally as a manufacturer of damp proofing and timber treatment products, the company now boasts some 250 different formulations, and the packaging makeover will be extended across the product portfolio in the coming months.