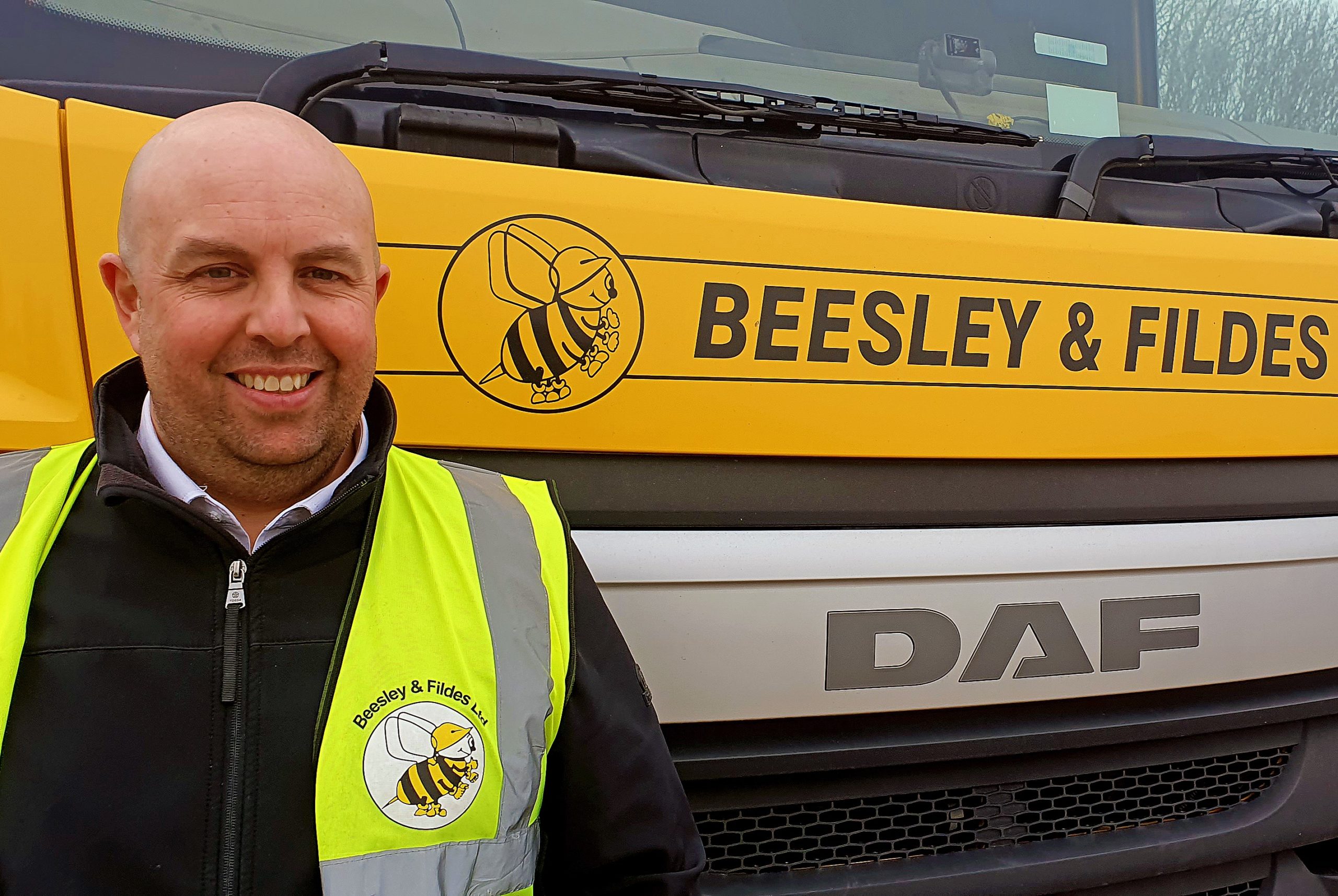
Nick Khan, Group Insulation and Drylining Manager at independent builders’ merchant Beesley & Fildes, discusses changes to Building Regulations (Part L) for England and how merchants and their customers are responding.
Changes to Building Regulations for the conservation of fuel and power (Approved Document Part L) set higher standards for energy efficiency in new homes. To meet these requirements, our customers must adapt too. New solutions may need to be sourced and installed — and merchants have a vital role to play.
The regulation’s overall aim is to reduce the carbon emissions of new homes by 31%. These requirements are set out in Part L Volume 1 and 2. Volume 1 covers new builds as well as extensions and changes to existing domestic properties. Volume 2 applies to non-domestic buildings.
Meeting the new rules will, in part, be achieved by improving the fabric of a building and that means new U-values for walls, roofs, floors, windows and doors on domestic properties. New homes will be assessed under a Standard Assessment Procedure (SAP) calculation called SAP 10.2, which succeeds SAP 2012 (9.92).
Questions raised
From our customers’ perspective, the changes have led to queries across two areas. The first relates to timescales and which projects will be affected. A common misconception is that the rules apply to all new builds and extensions constructed from 15 June 2022. However, planning applications approved before this date can be constructed under previous regulations — if the building work began before 15 June 2023.
The second area is the impact on building external walls, specifically the cavity size required. The average U-value that can be achieved with a traditional 100mm cavity is around 0.25 W/m2K. However, the update to Part L uses a ‘notional’ building recipe to set targets for carbon emissions, fabric energy efficiency and primary energy, which uses a U-value of 0.18 W/m²K for the walls.
To reach the notional target for a wall, a larger cavity of around 150mm can be used. Although this will require thicker and more expensive insulation than a 100mm cavity, customers will also need to spend more on larger lintels, cavity closers and wall ties creating higher ancillary costs. A larger cavity can also mean less room space.
On balance, most builders want to stick with the traditional 100mm cavity if possible, and are seeking new solutions that can help them cost-effectively meet the new regulations.
Keeping options open
In response, merchants are stepping up to advise customers on their options and provide a range of products that can help. By assessing all the different components that make up the wall and adjusting where needed, we can help them to meet the target U-value without changing the traditional 100mm cavity.
For example, using a very thermally efficient, lightweight block like Celcon Standard combined with EcoTherm full fill cavity insulation and a standard plasterboard on the internal walls will meet the new regulations. Alternatively, a medium density block such as Fibolite could be used with the same insulation plus an insulated plasterboard. This will enable builders to save on the block costs if preferred.
For those that decide to increase the cavity to 150mm, using Knauf DriTherm 32 in a 150mm thickness with a Celcon Standard block will meet the target U-value.
Ultimately, the decision will depend on the needs of the individual customer and the nature of the project, considering factors such as budget, labour and product lead times.
Spreading the word
As with all types of change, it takes time to adjust and with various solutions available for cavity walls, raising awareness is also key. At Beesley & Fildes we are in regular discussions with housebuilders to advise them on their options for meeting the new Part L. Our next step will be to visit customers in person to present the different constructions for both 100 and 150mm cavities.
By working in partnership and navigating the changes together, we can provide our customers with bespoke solutions that hit all the right targets.
A version of this article appeared in the June edition of PBM. Click here to read the full issue online via our website.
Beesley & Fildes has been touring the North West recently with its Roofing Roadshow. Throughout April, visitors were able to browse an extensive range of popular products while gathering advice from some of the industry’s leading suppliers including Velux, Dakea, Cromar, Cembrit, Lindab, Redland, Tapco, Marley, Timloc, Ariel, Iko, Warwick Windows, TLX Insulation, Kytun, Ultra Flex, BMI Group, North West Aluminium, KPB and Coxdome.
With dedicated roofing centres at its Huyton and Radcliffe branches, the independent merchant’s own go-to specialists were also available to offer guidance on their customers’ roofing requirements, including information around technical specifications and fitting instructions, while pointing them towards the most compatible products for the job in hand.
Speaking ahead of the Roadshow, the merchant’s Roofing Product Manager Steve Linacre said: “It’s a big event in our commercial calendar and is an ideal port of call for the region’s entire trade needs. People can rest assured when choosing our products that there is consistent availability, alongside technical support and guidance.”