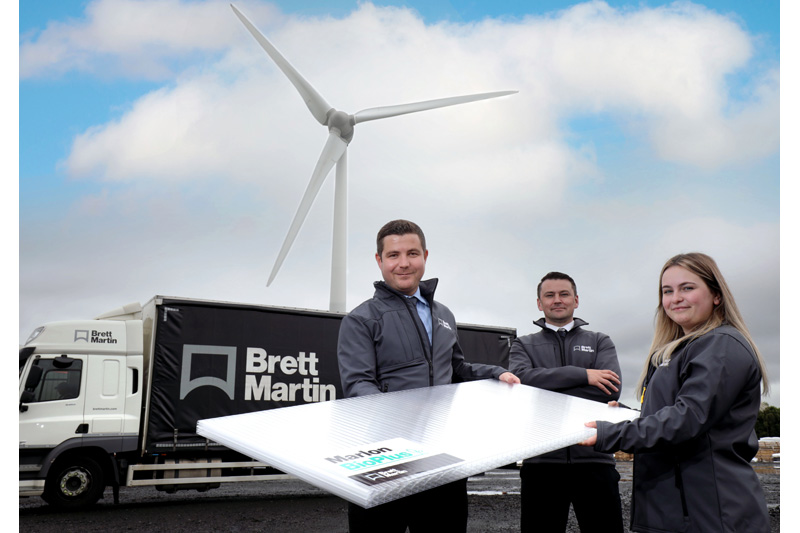
Brett Martin says it is set to reduce the carbon footprint of buildings with a “remarkable” new Polycarbonate glazing product largely based on bio-circular attributed material such as used cooking oil.
Called Marlon BioPlus, the new sheet offers “a major carbon footprint reduction” by cutting the use of fossil-based material by 70%. This raw material is said to deliver an 84% decrease in carbon emissions whilst Brett Martin achieves further reductions in carbon by producing the sheet using 100% renewable energy, generated at its own site.
Marlon BioPlus has already achieved International Sustainability & Carbon accreditation with ISCC Plus certification. ISCC PLUS is a globally recognised sustainability certification program for bio-based and bio-circular (recycled) raw materials with a focus on the traceability of raw materials within the supply chain.
What is said to make Marlon BioPlus unique is the combination of this certification and Brett Martin’s 100% onsite renewable energy, which together represents a huge step towards a zero-carbon polycarbonate sheet.
As the UK’s largest producer of polycarbonate roofing and facades Brett Martin supplies high profile projects as diverse as London’s Royal College of Art or Manchester’s Old Trafford stadium as well as a wide range of commercial and industrial buildings. This new low carbon alternative retains all the physical and performance properties of the company’s other Polycarbonate ranges and will be available to be specified in any Brett Martin’s Marlon polycarbonate multiwall, corrugated or flat sheets for use in roofs and walls.
Paul Martin, Brett Martin Director, said: “The drive for sustainable, carbon neutral plastic materials is progressing well, and our launch of Marlon BioPlus is the latest milestone in our journey to that end. Our extensive investment in renewable energy at our Mallusk site is unique in our industry and an important part of our plan. We extrude the sheet using energy generated from our own wind turbine and dedicated solar farm at Mallusk.
“This development of this new product reflects the newest technology in the plastic industry to introduce bio-based material. The process, known as mass-balancing, certifies the input of the material through the production system, similar to the way renewable energy enters the power grid. Importantly, the material is a recycled source and therefore the bio-based content does not compete with food production.”
He continued: “And because the substitution occurs at the earliest stage of the resin production process, all the visual and mechanical properties of the finished sheet remain completely unchanged. So, we anticipate strong demand for the product which is soon to be available to the market globally and we will begin to see it being used in all kinds of buildings soon.”