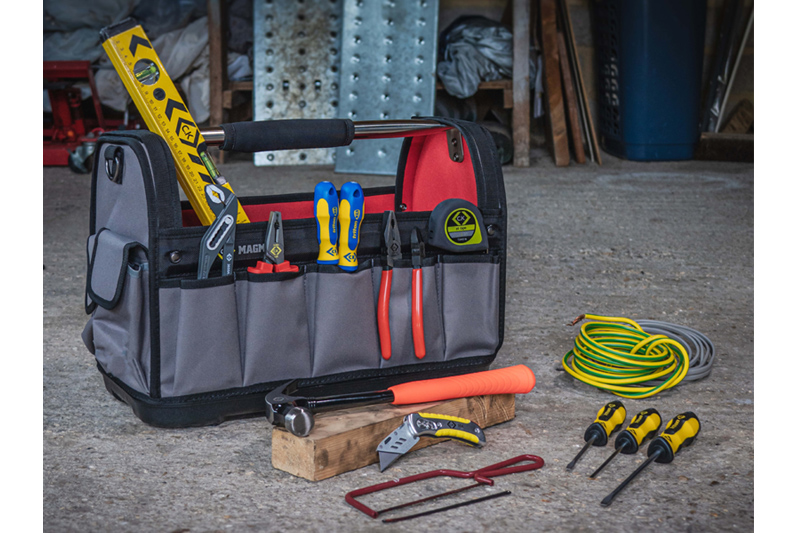
Brinley Buckley-Roberts, Brand Manager at Carl Kammerling International, the home of C.K Tools, discusses why premium hand tools are worth more than ever for merchant customers.
Many of us will struggle to remember a time when we tracked our spending as closely. Price hikes are diminishing profits, and each purchase is being made with extreme caution and forward planning. The cost-of-living crisis has altered the way we think about expenditure in both our personal and professional lives.
While cost cutting may have become a necessity for many, the old adage ‘buy cheap, buy twice’, has never been truer. Tool choice always requires careful consideration. For any builder, an inadequate tool can lead to downtime, a slow work rate, and ultimately an un-forecasted replacement purchase, all impacting bottom lines. A tool that delivers a poor finish can lead to reputational damage and kill repeat business. At their worst, poor tools can be unsafe.
Perhaps now more than ever is the time for them to invest in premium tools. In challenging times, it makes sense to be fully equipped to deliver speedy, top-quality results, safely, and without the threat of unexpected expenditure. Investing in premium hand tools can really make a difference in both the short and long-term.
So, what should you advise your customers look for when purchasing tools? There are several elements to consider, and a few key areas that separate premium tools from the rest: the R&D process; the source of the materials; the engineering and manufacturing procedures; the quality control and accreditation. Each element undergoes a constant review as new materials, manufacturing techniques, or industry requirements are uncovered, with the effectiveness, durability and safety of the products always top of mind.
Research and development can mean many things but for C.K Tools this means listening intently to what the industry is asking for. We utilise a panel of professionals to not only find solutions to problems, but to also find the existing product evolutions that will make the job that much more efficient. From there, our NPD team goes into design and considers the aesthetics, the ergonomics, and of course the materials. There’s no product without a clear rationale; each one is meticulously planned, refined, prototyped and tested.
Material choice is of great importance to C.K Tools and has contributed considerably to the reputation we’ve built over more than 200 years. In the most part we procure our steel from and manufacture our products in Germany, in particular the North Rhine, which is world-renowned for its steel production. The region’s steel has varying levels and mixes of chromium, which has excellent corrosion resistance, vanadium, which works as a deoxidiser and reduces wear, and molybdenum, which when combined with chromium gives greater strength and impact resistance.
Not content with its premium grade steel, the North Rhine is also known as the industrial heartland for tool manufacturing. The steel mills, chemical and water treatment businesses, and manufacturing plants all reside there and have developed great ways of collaborating over the years to ensure that the potential of the raw material is not lost through the processing and engineering stages.
C.K Tools has been working with its current manufacturing partners since 1904 and there’s a reason for it; in today’s market it is very rare that products are manufactured to the very peak of excellence but with German engineering practices that’s a given.
Precision engineering requires a number of inputs and with hand tool manufacturing that starts with the quality of the die — the item used to stamp the shape of the tool in the steel. Utilising a mixture of CAD and CNC, dies can be cut to within a tolerance the equivalent of a human hair, delivering a near perfect product with every stamp.
Other engineering techniques are then used to ensure our products offer outstanding longevity. Induction hardening is a process we use to ensure that parts of products — such as the jaws on pliers — are hardened to withstand heavy usage and ensure long-term performance. It involves electromagnetically heating up the steel and then rapidly cooling it to maintain the desired properties.
The precision engineering techniques don’t stop at the steel; hand tools must be inherently comfortable and safe to handle. To ensure this, every single screwdriver handle is injection moulded directly to the steel, giving the ultimate torsion-proof bond for increased reliability, durability, control and comfort. These touches all contribute to an easier and faster working experience: profitable efficiency.
Paying a premium price for a tool may seem counter-intuitive during a cost-of-living crisis, but it’s important to understand what your customers are paying for and how it will impact their work. C.K Tools understands the requirements of each and every job; and is unwavering in its pursuit of precision engineering the perfect product to sell and to use. Yes, German engineered products come with a premium, but rest assured, they’ll be the best investments one can make.
Click or tap the following link for further information on CK Tools.