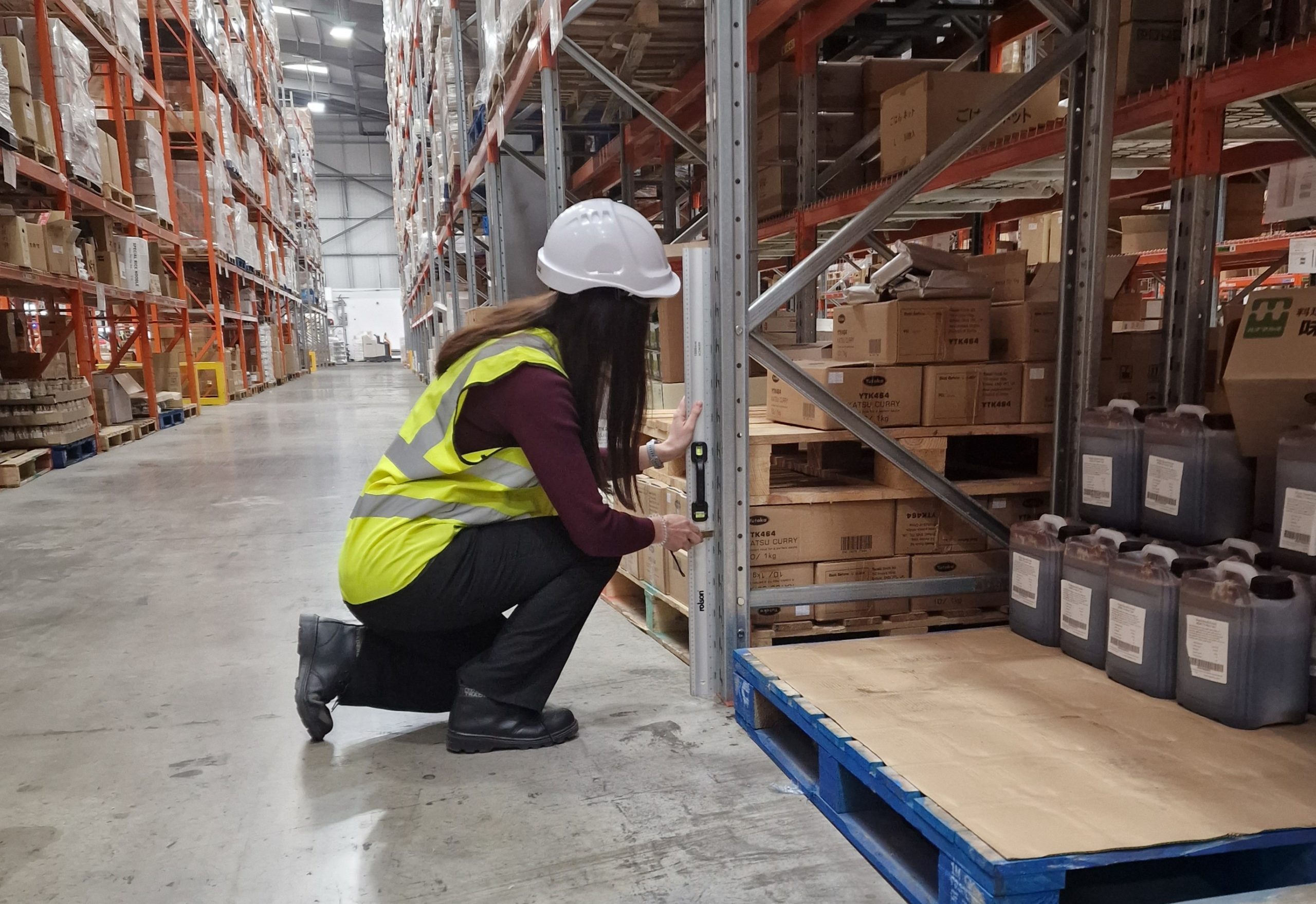
If you’ve got racking at your branch, you’re going to need the correct advice. Nick Betteley, President at the Storage Equipment Manufacturers’ Association, explains how SEMA can help merchant businesses ensure their racking is safe.
When racking works as intended, it can perform multiple tasks. It can help to increase your stock requirements and efficiency, ensure better inventory management, reduce costs and keep your employees and customers safe.
But, as a complex piece of equipment, how can you ensure your racking is safe and compliant? Failing to implement best practices throughout the lifetime of your racking can come at a financial, reputational and safety cost you don’t want to ignore.
This is where SEMA can help. As the leading voice for the storage equipment industry, we provide impartial advice on racking dos and don’ts:
Know your racking regulations: In any business, there are plenty of health and safety regulations to follow, covering everything from manual handling to working at height.
However, did you know there are specific safety guidelines for racking systems? The HSE’s HSG76 Warehousing and Storage: A Guide to Health and Safety outlines an owner’s responsibility to implement preventive measures to avoid hazards. You also have SEMA codes, essential for anyone responsible for storage equipment; these standardised documents cover the key stages of your racking’s lifetime.
Following these documents is not a legal requirement, but implementing their steps is normally enough to generally satisfy health and safety requirements.
“Failing to implement best practices throughout the lifetime of your racking can come at a financial, reputational and safety cost you don’t want to ignore.”
Chose reliable suppliers: When getting racking, you need a supplier who understands your business requirements and works to the latest industry standards. Yet, in a crowded market, how do you know which supplier to trust?
SEMA Members include industry-leading storage equipment manufacturers and suppliers. And membership with SEMA isn’t bought — it’s earned. Members must pass an independent audit that checks the quality of their work, that legal and insurance documentation is in place, and that their work meets the highest industry standards.
Racking training: To reduce unnecessary repair costs and uphold the safety of your equipment, your racking must continue functioning as intended. Any damage to the structure can significantly reduce its load-carrying capacity and repairs must be undertaken quickly.
Your employees are the first line of defence when reporting issues — but this is only possible if they know what to look for. A course like our Rack Safety Awareness programme, referenced in HSG76, provides advice and guidance on correct loading methods and damage identification.
This training also prepares a nominated member of your team for undertaking Regular Inspections. Usually conducted weekly/monthly, this visual inspection checks for damage, correct usage and ensures maximum loads are not exceeded. They also make a formal report of their findings and required actions which is part of your official maintenance documentation.
The importance of inspection: At least once a year, your racking needs an Expert Inspection by a trained professional such as a SEMA Approved Rack Inspector (SARI). The inspector issues a written report outlining observations, recommendations and proposals for required remedial work.
Not all inspections are equal. A “damage only” inspection provides a list of damaged items and possibly their location, while a SARI report offers far more detail, including colour-coded damage and repair timescales.
For more advice, contact SEMA by emailing enquiry@sema.org.uk or visit www.sema.org.uk